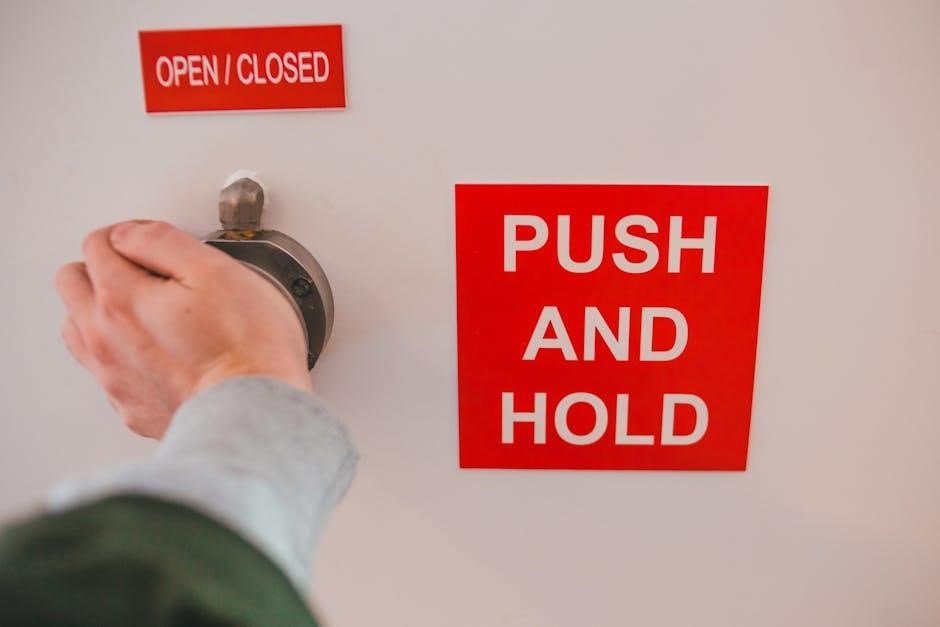
Welcome to the PowerFlex 4 User Manual, your comprehensive guide to installing, configuring, and operating the Allen-Bradley PowerFlex 4 adjustable frequency AC drive. This manual provides essential information for safe and effective use, ensuring optimal performance in various industrial applications. Refer to the official Rockwell Automation publications for detailed specifications and troubleshooting support.
1.1 Overview of PowerFlex 4 Adjustable Frequency AC Drive
The PowerFlex 4 Adjustable Frequency AC Drive is a high-performance motor control solution designed by Allen-Bradley, a Rockwell Automation brand. It offers precise speed and torque control for industrial applications, featuring a compact design and advanced functionalities like Safe Torque Off (STO). Suitable for a wide range of applications, the drive provides reliable operation, energy efficiency, and user-friendly interfaces for easy configuration and monitoring.
1.2 Important Safety Information and Precautions
Read this manual carefully before installing or operating the PowerFlex 4 drive. Ensure proper grounding to prevent electrical hazards. Avoid unauthorized modifications or repairs. Only qualified personnel should perform installation, configuration, or maintenance. Use approved components and follow safety guidelines to prevent injury or equipment damage. Always refer to the official Rockwell Automation publications for detailed safety protocols and precautions. Proper adherence ensures safe and reliable operation.
Installation and Setup of PowerFlex 4
Follow the installation guidelines carefully to ensure proper wiring and setup of the PowerFlex 4 drive. Refer to the official Rockwell Automation manual for detailed instructions.
2.1 Physical Installation and Wiring Guidelines
Ensure proper installation and wiring of the PowerFlex 4 drive by following the guidelines in the Rockwell Automation manual (22A-UM001). Mount the drive securely and connect input power, motor, and control signals correctly. Proper grounding and shielding are essential to prevent noise interference. Always use recommended components and follow safety precautions to avoid damage or hazards. Refer to the manual for detailed wiring diagrams and installation best practices.
2.2 Initial Configuration and Parameter Settings
Configure the PowerFlex 4 drive using the control panel or software tools. Set motor nameplate parameters, select the control mode, and adjust speed references. Enable safety features like Safe Torque Off (STO) if required. Refer to the Rockwell Automation manual (22A-UM001) for detailed parameter descriptions. Save configurations to ensure proper operation. Consult the manual for troubleshooting common issues during setup and for advanced parameter tuning options to optimize drive performance for specific applications.
Understanding PowerFlex 4 Features and Functionalities
Explore the PowerFlex 4’s advanced features, including adjustable frequency AC drive operation and Safe Torque Off (STO) functionality. These features enhance motor control, safety, and efficiency.
3.1 Adjustable Frequency AC Drive Operation
The PowerFlex 4 operates by adjusting the frequency and voltage supplied to a motor, enabling variable speed control. This functionality optimizes motor performance, reduces energy consumption, and minimizes wear. The drive supports various control modes, including Volts per Hertz and sensorless vector control. It also integrates advanced features like Safe Torque Off (STO) to enhance safety. Refer to the manual for detailed configuration and operational guidelines to maximize efficiency and reliability in industrial applications.
3.2 Safe Torque Off (STO) Functionality
The PowerFlex 4 incorporates the Safe Torque Off (STO) feature, designed to safely remove power from the motor while maintaining control. This functionality is essential for industrial applications requiring enhanced safety and compliance with international standards. STO ensures the motor stops without generating torque, ideal for maintenance and emergency situations. Proper configuration and testing are crucial for reliable operation. Refer to the manual for detailed setup and implementation guidelines to ensure optimal performance and safety.
Parameters and Configuration Details
This section covers key parameters for motor control and optimization, as well as advanced configuration options for custom applications, ensuring precise drive performance and flexibility.
4.1 Key Parameters for Motor Control and Optimization
Adjust acceleration and deceleration times, torque limits, and voltage/frequency ratios to match motor characteristics. Configure motor nameplate data for accurate control. Set speed and torque references, enabling precise motor operation. Parameters like motor flux and slip compensation ensure optimal performance. Proper setup of these parameters enhances motor efficiency, reduces wear, and prevents overheating. Refer to the manual for detailed instructions on configuring these settings for specific applications.
4.2 Advanced Configuration Options for Custom Applications
Customize your PowerFlex 4 drive with advanced settings for unique applications. Utilize custom motor profiles, adaptive tuning, and application-specific parameters to optimize performance. Adjust speed and torque limits, acceleration/deceleration rates, and voltage/frequency curves for precise control. Enable specialized modes like vector control or sensorless operation for demanding applications. Configure input/output signals and communication settings to integrate with industrial systems. These options allow tailored solutions for complex requirements, ensuring enhanced productivity and reliability in diverse industrial environments.
Troubleshooting and Maintenance
Troubleshoot common faults and perform routine maintenance to ensure optimal performance. Identify error codes, check connections, and update firmware as needed. Refer to the official manual for detailed guidance.
5.1 Common Faults and Error Codes
The PowerFlex 4 drive may display error codes indicating issues like overcurrent, overheating, or communication faults. Error codes such as 13000-13999 are documented in the manual. LED indicators on the drive provide visual alerts. Common faults include power supply issues, motor overloads, or incorrect parameter settings. Resetting the drive or updating firmware may resolve some errors. Always consult the official PowerFlex 4 User Manual for detailed troubleshooting steps and safe resolution procedures.
5.2 Maintenance and Diagnostic Procedures
Regular maintenance ensures optimal performance of the PowerFlex 4 drive. Check connections, clean cooling systems, and verify parameter settings. Use diagnostic tools like the control panel or software to monitor operation. Reset or update firmware as needed. Consult the PowerFlex 4 User Manual for detailed maintenance schedules and diagnostic procedures. Always follow safety guidelines and manufacturer recommendations to prevent damage and ensure reliable operation. Proper care extends the drive’s lifespan and minimizes downtime.
User Interface and Navigation
The PowerFlex 4 features an intuitive control panel and display for easy navigation. Software tools provide advanced programming and monitoring capabilities, ensuring seamless operation and customization of drive settings.
6.1 Navigating the Control Panel and Display
The PowerFlex 4 control panel features a user-friendly interface with navigation buttons and a clear display. The menu structure allows easy access to parameters, status monitoring, and diagnostics. Use the navigation keys to scroll through options and adjust settings. The display provides real-time data on drive operation, fault codes, and configuration status. Refer to the manual for detailed instructions on utilizing these features effectively for optimal drive performance and troubleshooting.
6.2 Using Software Tools for Programming and Monitoring
The PowerFlex 4 supports advanced software tools for programming and monitoring, enhancing drive configuration and performance. Rockwell Automation’s software solutions enable parameter adjustments, real-time monitoring, and diagnostic capabilities. Utilize these tools to optimize drive settings, troubleshoot issues, and ensure seamless integration with industrial systems. Refer to the user manual for detailed guidance on software installation, operation, and compatibility to maximize the drive’s functionality and efficiency in various applications.
Application Examples and Best Practices
Explore typical industrial applications of the PowerFlex 4, such as controlling pumps, conveyors, and HVAC systems. Follow best practices for installation, configuration, and maintenance to optimize performance and longevity.
7.1 Typical Industrial Applications of PowerFlex 4
The PowerFlex 4 is widely used in various industrial applications, including pump control, conveyor systems, and HVAC systems. Its versatility makes it suitable for machinery and motion control, ensuring precise speed regulation and energy efficiency. Additionally, it is applied in material handling and water treatment systems, where reliable motor control is essential. The drive’s compact design and robust features make it ideal for a broad range of automation tasks.
7.2 Best Practices for Optimizing Drive Performance
To optimize the performance of your PowerFlex 4 drive, ensure proper installation and wiring as per the manual. Regularly update firmware and calibrate parameters for precise motor control. Monitor operating conditions and perform routine maintenance to prevent faults. Use official Rockwell Automation software tools for programming and monitoring. Refer to the user manual for specific guidelines and safety precautions to maximize efficiency and longevity of the drive in industrial applications.
Additional Resources and References
Consult the official PowerFlex 4 User Manual (Publication 22A-UM001) and Rockwell Automation’s online support for detailed technical documentation, troubleshooting guides, and software tools to enhance your experience.
8.1 Official PowerFlex 4 User Manual and Publications
The official PowerFlex 4 User Manual (Publication 22A-UM001) provides detailed instructions for installation, configuration, and troubleshooting. It covers key parameters, safety guidelines, and advanced features. Additional publications, such as wiring and grounding guides, are available on Rockwell Automation’s website. These resources ensure comprehensive support for optimizing and maintaining your PowerFlex 4 drive effectively in industrial applications.
8.2 Online Support and Technical Documentation
Rockwell Automation offers extensive online support for the PowerFlex 4, including downloadable manuals, troubleshooting guides, and technical bulletins. Visit their official website for access to Publication 22A-UM001 and other resources. Online forums and technical documentation provide additional assistance for addressing specific challenges and optimizing drive performance. These tools ensure users have comprehensive support for their PowerFlex 4 applications at their fingertips.
This concludes the PowerFlex 4 User Manual. It provides essential insights into installation, configuration, and troubleshooting, supported by Rockwell Automation’s official resources for further learning.
9.1 Summary of Key Concepts and Takeaways
The PowerFlex 4 User Manual offers a detailed guide to installing, configuring, and troubleshooting the drive. Key topics include safety precautions, parameter settings, and advanced features like Safe Torque Off. The manual emphasizes proper wiring and grounding to ensure reliable operation. For optimal performance, users should consult Rockwell Automation’s official documentation and utilize software tools for programming and monitoring. Regular maintenance and adherence to best practices are crucial for longevity and efficiency.
9.2 Encouragement for Further Exploration and Learning
Exploring the PowerFlex 4 beyond this manual is highly encouraged to maximize its capabilities. Dive into Rockwell Automation’s official resources, such as the PowerFlex 4 User Manual (Publication 22A-UM001) and online technical documentation, to gain deeper insights. Engage with online forums and training materials to enhance your understanding of advanced features like Safe Torque Off and custom application configurations. Continuous learning will empower you to optimize drive performance and stay updated with the latest industry advancements.